ピッキング/アソートソリューション
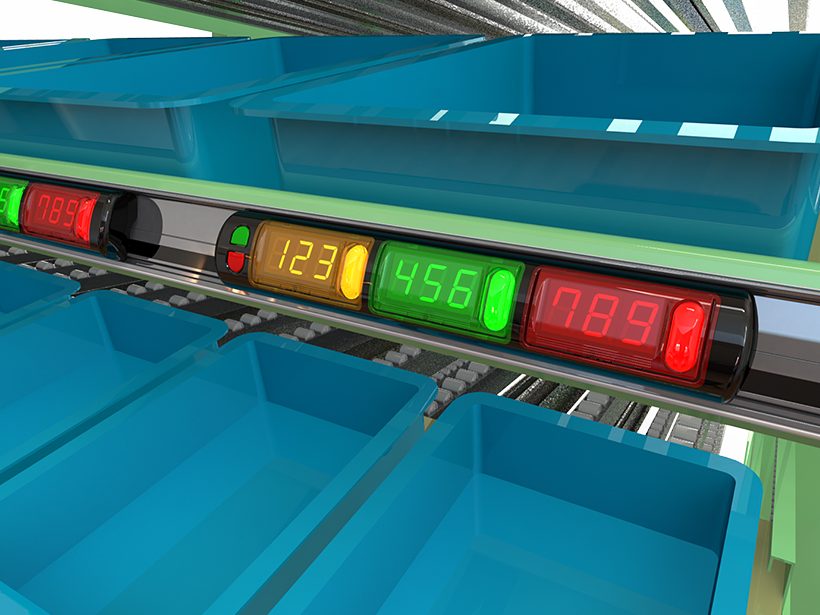
作業ミスを軽減し、ピッキングや仕分けの効率化を
図るソリューションをご紹介します
こんなお悩みはありませんか
-
アイテムの種類が多く、探す手間がかかる
-
採用難で人員を増やすことが難しい
-
類似アイテムが多く、ピッキングミスが頻発している
-
スポットワーカーを活用しており、単純簡単作業を提供したい
-
ピッキングの手順が多く、教育に時間がかかる
-
広い敷地の移動で作業者に負担がかかっている
-
ロボット等の自動化へのハードルが高い
実現する改善ポイント
-
01
ピッキング・アソート精度の向上
デジタルピッキングやプロジェクションピッキングにより、人為的な作業ミスを大幅に減らし、出荷品質を向上させます。
-
02
ピッキング・アソート効率の改善
物流分析を元に、最適化されたピッキング・アソート動線とリスト不要のデジタル化により、作業時間を短縮し、人員配置を適正化できます。
-
03
多種多様な業態や荷姿に柔軟に対応
豊富なピッキングソリューションラインナップを活かし、多種多様な業態や荷姿に柔軟に対応します。Eコマースから店舗向け出荷、大口出荷まで、お客様のニーズに合わせた最適なピッキングやアソート方式をご提案します。
-
04
作業者の負担軽減
ピッキングカートを活用した運用やDPS、DAS、PPS🄬の導入で、作業者は物の位置を記憶する必要がなく、誰でも考えずに作業が可能です。結果、作業者の肉体的・精神的負担を軽減し、働きやすい環境を実現します。
-
05
コスト削減
伝票が不要となり、ペーパーレス化しながら、庫内作業のシステム化を確立できます。作業効率の向上と省人化により、人件費や庫内作業コストの削減が可能です。
-
06
スケーラビリティの確保
AIOI製のハードと拡張性の高いソフトウェアで、将来的な物量増加や業務変化に対して、システムの拡張性を確保できます。また人による作業支援やロボットと人を組み合わせた作業支援など現場に合わせて柔軟に再設計・最適化をご提案します。
提案事例
AIOIは現場の物流分析を実施、課題を洗い出し、お客様に最適なソリューションをご提案します。
医薬業界 事例 既存DPSのリプレース例
他社既存システムが現在の現場運用に合わなくなり、システム変更の必要性と効率化が迫れていた医薬品メーカーA社様の課題を解決した導入提案の事例をご紹介します。
課題
-
物量の増加による工数増加
-
卸向け大量と医療機関向け少量の混在
-
システムの老朽化によるトラブルの懸念
提案内容
-
物流分析に基づくご提案お困り事のヒアリングと調査
-
5名同時別オーダー作業の出荷検品システムとの並行導入
-
豊富な実績に基づき最新システム導入
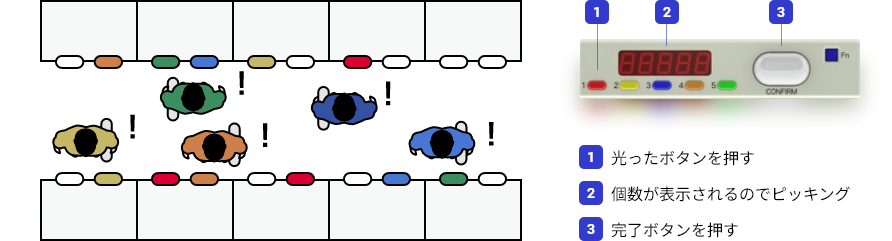
導入システム
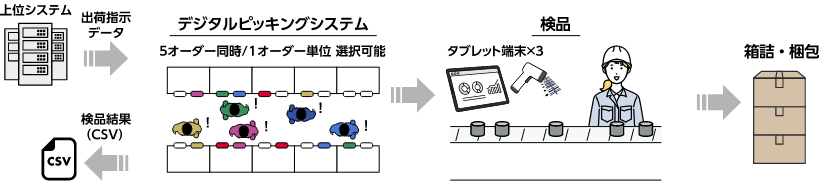
効果
-
時間短縮により繁忙期の出荷も残業・増員無く可能に!
-
人時生産性15%アップし、作業員の歩行距離が40%削減!
書籍業界事例 リストピッキングからデジタルピッキングへの切り替えで生産性向上
約1,600アイテムから、紙の注文書を見ながら「書店出荷先別」に手作業でピッキングしていたが、物量が多くなるにつれ、取り間違いや、梱包漏れが多くなってしまったことからデジタルピッキングの導入を検討されていました。
課題
-
手作業によるリストピッキングのため、取り間違いや梱包漏れが多い
-
ベテラン作業者への依存が高く、物量が増えるにつれ、作業員を増員しているため現場リーダーの負担がかかっている
提案内容
-
ピッキング点数が多い場合、書籍重量が増えてしまう為、運ぶ際は自動コンベアを利用して作業者の負担を減らす
-
該当棚がわかるように棚単位にパトライトを設置
-
4桁まで表示する事ができるデジタルピッキングを導入し、点灯色は赤色のみとする
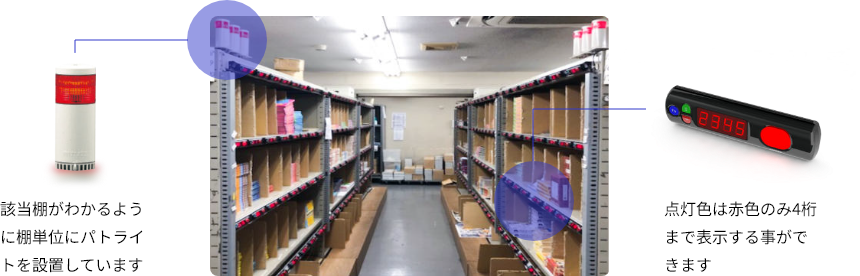
ポイント
・表示器の取付、レイアウト変更が容易である
・極性の無い2芯ケーブル仕様により、誤設置時によるショートを防止できる
効果
-
取り間違いによる手戻り作業時間の大幅削減を実現
-
10数名の作業人数で約8時間かかっていた作業時間が10名で約5時間に!
-
誰でも作業ができるようになり、現場リーダーの負担削減や人件費含む物流コストの抑制につながった
雑貨業界 A・B・C品の簡単仕分けシステムを確立。効率17%UPと人員削減
複雑化するA・B・C品仕分けを誰でも簡単にできる仕組みををご提案。作業効率17%アップ、作業人員の削減も実現。
課題
-
商品点数が多く、商品ごとの出荷頻度もバラつきが多いため、作業者の歩行距離が多く、生産性の改善を阻害していた
-
ベテラン作業員に頼らないスマートなシステムを実現する必要があった
-
作業人員の削減を早急実現する必要があった
提案内容
-
製品のヒット率に対して物流分析を行い、A品、B品、C品に保管エリアを分ける
-
コンベアを使用して作業することで歩行同線が短縮
-
A品エリアでは1間口ずつにデジタル表示器を設置
-
B品、C品エリアは棚に代表表示器を設置し、コストを削減
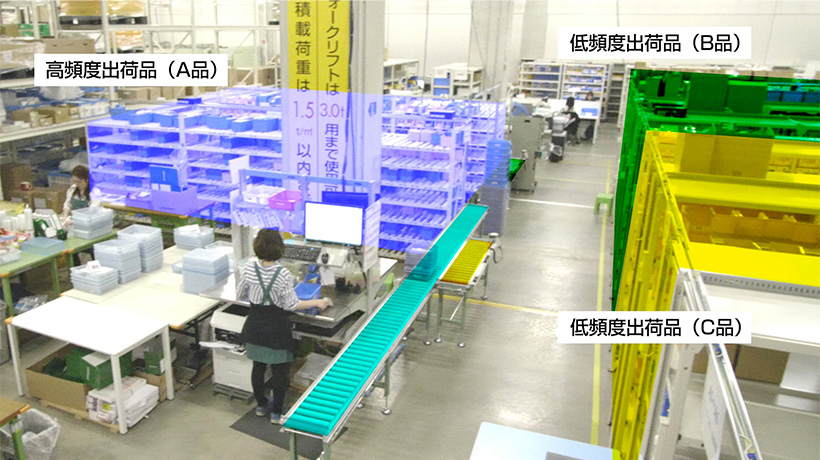
高頻度出荷品(A品)はコンベヤを中心にフローラックを配置、低頻度出荷品(BC品)は中量ラックとコンベヤで構成。作業動線を確保し、現場作業の負担軽減と作業品質の向上をもたらすDPSシステムをご提案
効果
-
物流分析を元にした現場設計。歩行同線短縮による作業効率が17%アップ
-
表示器の指示に従い作業を行うシンプルな仕組みなため、作業者に優しく、誰でも簡単にできるピッキングシステムが実現
-
作業人員の削減に成功