メンテナンス部品仕分けで、修理遅延防止と持続可能な現場を実現
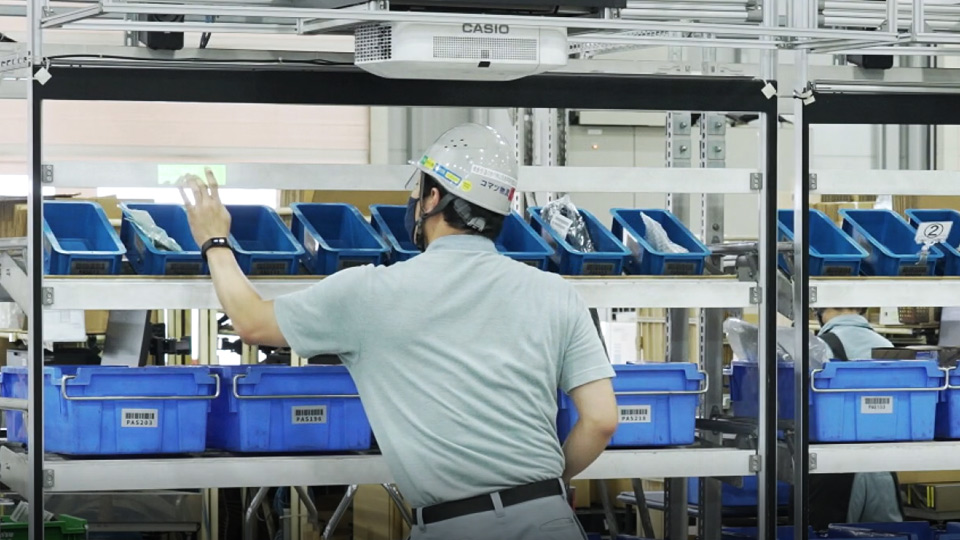
コマツ大阪工場様
導入事例の紹介動画
センサー方式のプロジェクションピッキングシステム🄬PPSを導入
プロジェクションピッキングシステム導入により作業性UP+ポカミス防止
- 導入の背景
-
-
現場直送の場合、出荷先ごとに間口が多く、更に棚が必要、広いスペースとより多くの人員が必要になる。
-
投入間口が多いため、仕分けする間口を探すのに時間がかかる。
-
伝票と棚番号を見比べて仕分けを行っているため、部品の入れ間違いによる仕分けミスが発生する。
-
- 導入の決めて
-
-
プロジェクターを使った新しいシステムだという点と表示器では実現しなかったポカヨケ機能
-
プロジェクターによる自由なレイアウト変更が可能
-
- 導入後の効果
-
-
出荷作業が2日かかっていたのが翌日配達が可能に
-
作業スペースを縮小
-
作業の標準化で生産性向上
-
人的作業ミスを激減
-
導入の背景
現場直送の場合、出荷先ごとに間口が多く、更に棚が必要、広いスペースとより多くの人員が必要になる。
ユーザーからの多種多様なオーダーに対し、発注から納品までのリードタイムを短縮し、サービスを向上する必要があった。
投入間口が多いため、仕分けする間口を探すのに時間がかかる。
本日発送予定のすべての客先に向けて間口を用意しその間口を探す必要があったがバッチを区切ることにより間口数を減らし作業者の探す時間の短縮に成功した。
伝票と棚番号を見比べて仕分けを行っているため、部品の入れ間違いによる仕分けミスが発生する。
伝票にはキーになる番号他たくさんの情報が載っている為作業者が間違ってしまう事が多々あった。
導入の決めて
プロジェクターを使った新しいシステムだという点と表示器では実現しなかったポカヨケ機能
デジタル表示器を使用している現場はたくさんみるがプロジェクターを使用した仕分けシステムはほかにない。コマツ関係者が見学にくるので驚かれるようなシステムにしたかった。
プロジェクターによる自由なレイアウト変更が可能
有線表示器だと間口サイズが変わると機器の据え付け直しが必要だがプロジェクターだとシステム変更だけで対応可能
導入後の効果
出荷作業が2日かかっていたのが翌日配達が可能に
従来補給部品の出荷は最短でも2日かかかっていたのが、仕分け作業を効率化することで修理を長引かせることなく翌日配達が可能に。
作業スペースを縮小
現場直送の場合、出荷先ごとに間口が多く、更に棚が必要、広いスペースとより多くの人員が必要になるが、PPS🄬の運用でバッチで区切る事によってスペースをフローラック2棚に縮小できた。
作業の標準化で生産性向上
PPS導入により仕分け作業の簡易化が実現され、作業者による作業スピードのバラつきがなくなり、作業を標準化することで、仕分け業務の生産性がアップした。
人的作業ミスを激減
伝票と棚番号を見比べて仕分けを行っているため、部品の入れ間違いによる仕分けミスが発生していたが、PPS🄬のポカヨケ機能により、作業者が入れた手の位置を検知し、警告音と光でミスを知らせ、仕分けミスが激減した。