昨今、様々な業種で進んでいるDXですが、品質担保が最大の使命である品質保証業務では効率より確実性が重視されるため、品質低下のリスクが完全に排除された状況でないと新しい方法を取り入れることができず、一般的にDX化が遅れがちでした。しかし、労働生産人口の減少が懸念される現在、品質担保と効率化の両立を図ることは急務です。そこで、日立製作所大みか事業所では6つの品質保証業務のデジタライゼーションを実証実験し、その一部を本格運用しています。
ヒューマンエラーのリスクを排除する「落穂拾い」の精神
日立製作所の品質保証部門では上下水道、発電所・変電所、製鉄所、そして交通といった社会インフラを支える制御盤とそれらを組み合わせた監視制御システムの品質保証を行っています。製品が完成すると図面通り製作されているか確認し、お客さまの現場でも据え付けした後、試運転により性能が満たされていることを確認します。
人が行う仕事には必ずヒューマンエラーのリスクがありますが、品質保証業務を行う品質保証部門では些細なミスが大きなトラブルの要因となることもあり、徹底的に排除する必要があります。そこで、人に頼るのではなくITツールを使った取り組みが開始されました。名付けて「品証デジタライゼーション」プロジェクトです。
日立製作所では、「失敗から経験を拾う」ことで失敗の再発防止を徹底する、という意味合いの「落穂拾い」の精神が継承されています。お客さまの立場で、お客さまとのお約束を守ることに主眼を置き、問題が本質的に解決するまで原因を徹底的に究明する、そうしたDNAが強く根付いています。「人は失敗を免れ得ない」という前提のもと、ヒューマンエラーのリスクを徹底的に排除するにはどうしたらよいか。このプロジェクトは、そうした日立製作所の企業文化から生まれた仕組み作りと言えます。
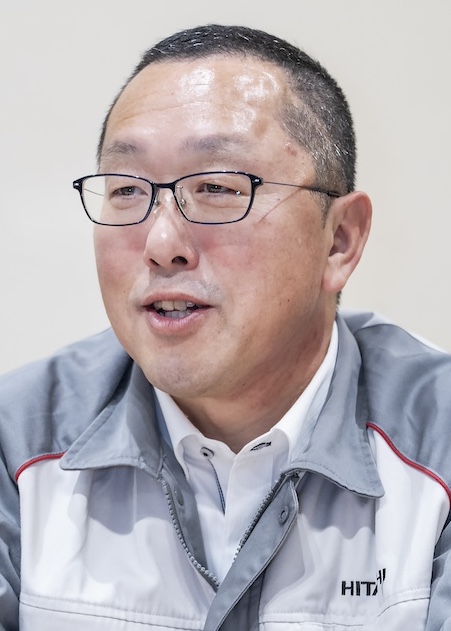
制御プラットフォーム品質保証本部
制御プラットフォームQAセンタ
プロセス管理グループ
新岡 正彦
品質を担保したまま効率アップを図る6つの取り組み
「品証デジタライゼーション」プロジェクトでは、品質コンプライアンス強化や生産性向上、そして現地作業高度化を目的に、6つの取り組みを行いました。
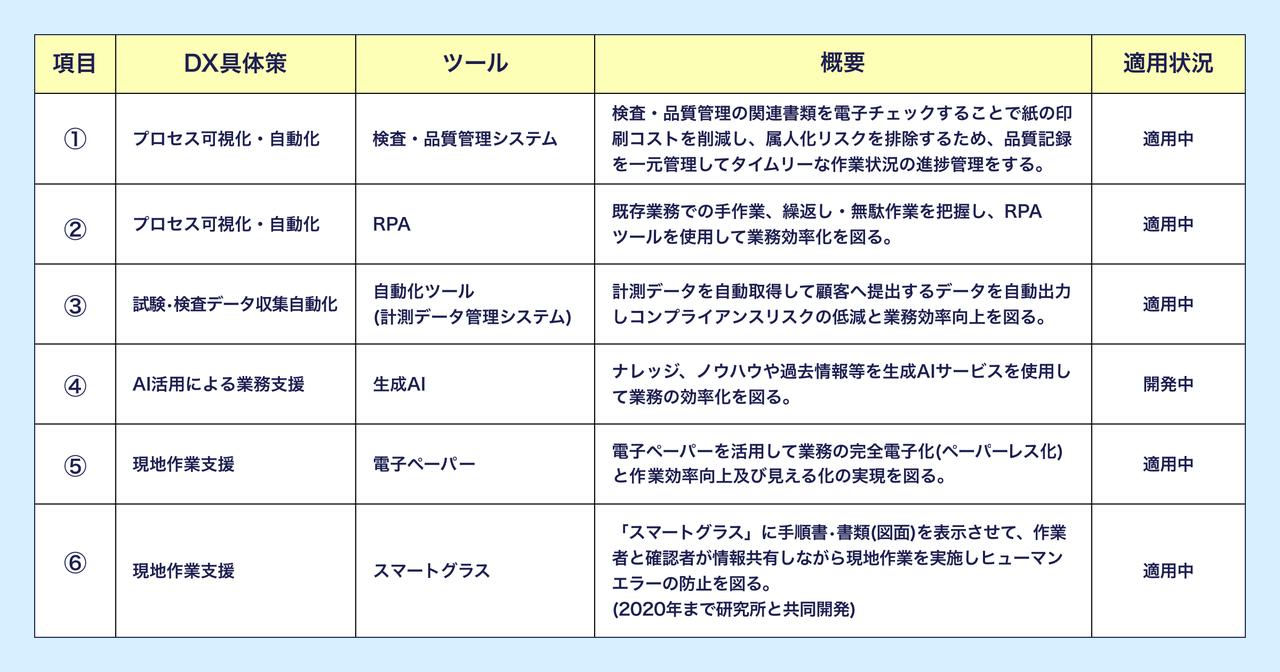
紙から電子データに移行、品質記録を一元管理
①の検査・品質管理システムの導入目的は、検査におけるコスト削減とリスク管理やコンプライアンス強化です。紙の資料は電子データに変わり、現場ではタブレットを持ちながらの作業に変わりました。(2023年度から本格運用)
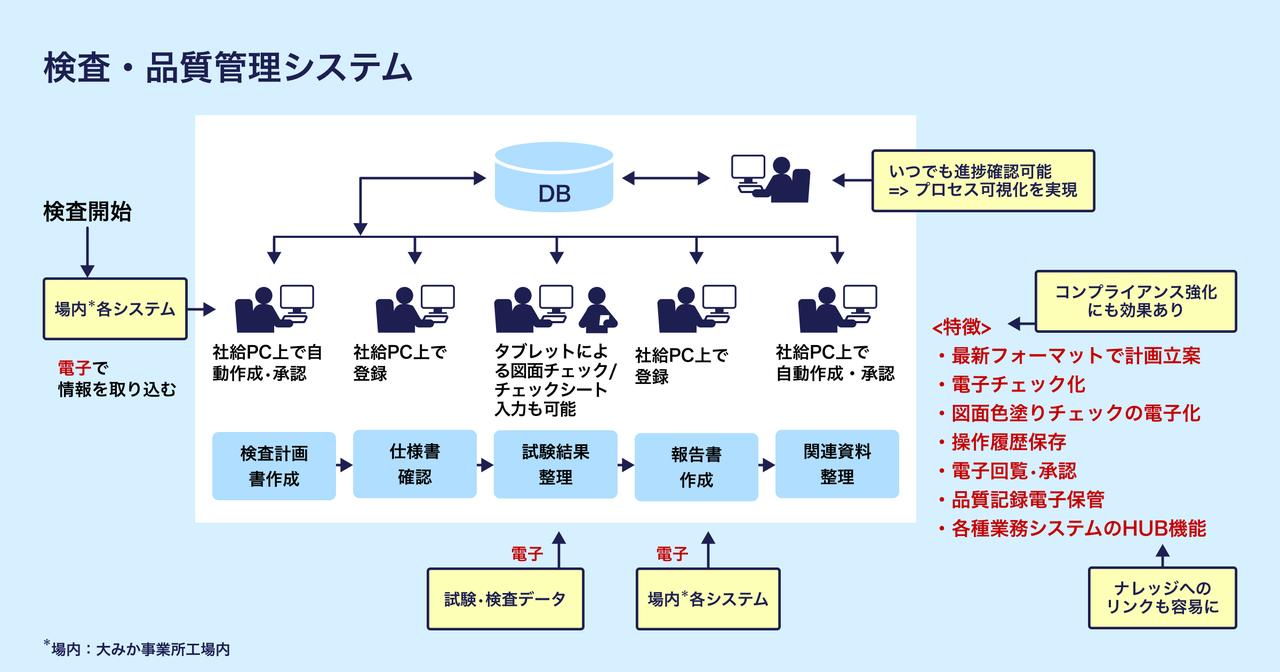
実際の作業の様子
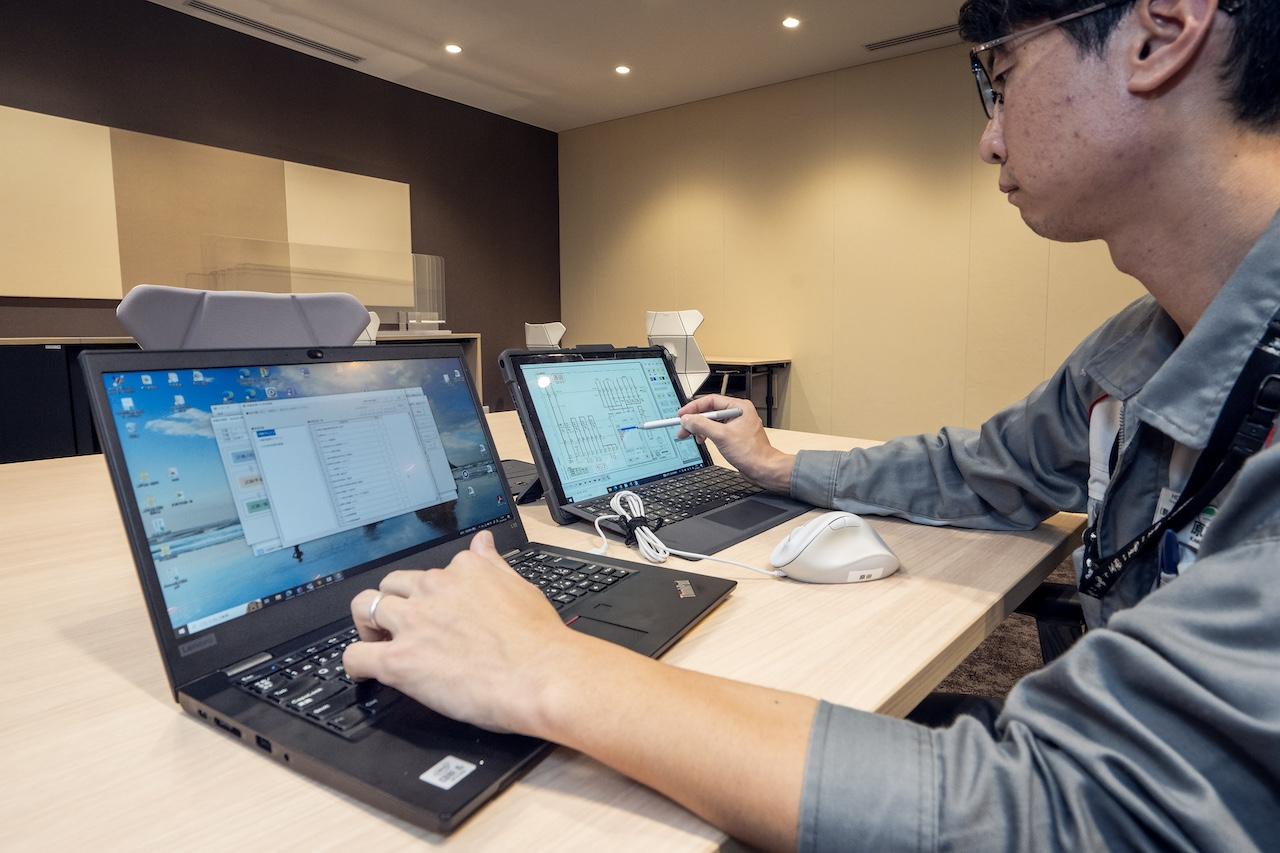
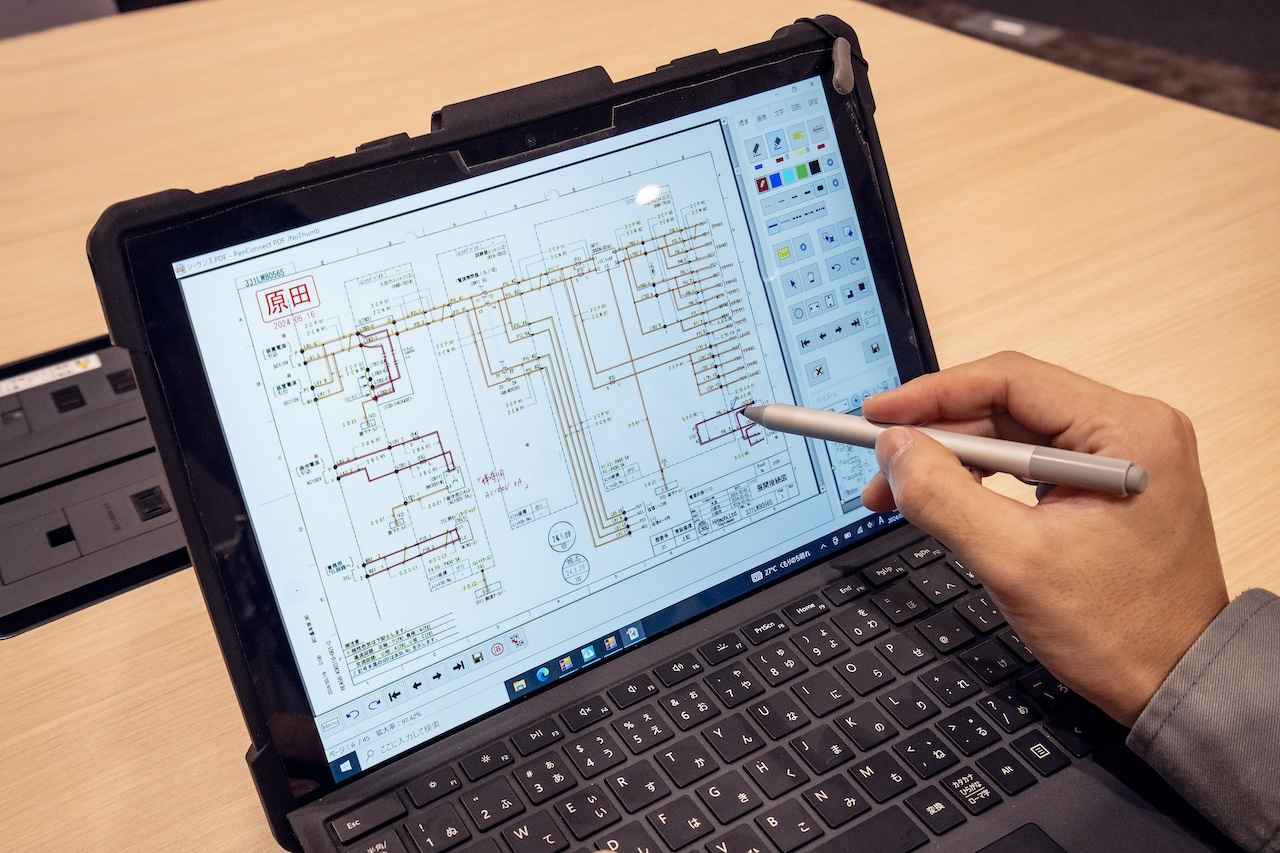
スマートフォンアプリの活用で棚卸を簡便化
②のRPAツールの導入目的は、ルーチンワークの効率化です。例えば少額固定資産の棚卸では、iPhoneの写真撮影アプリで棚卸対象品に付いている二次元コードを読み取るシステム導入など複数のルーチンワークを効率化しました。(2024年度から本格運用)
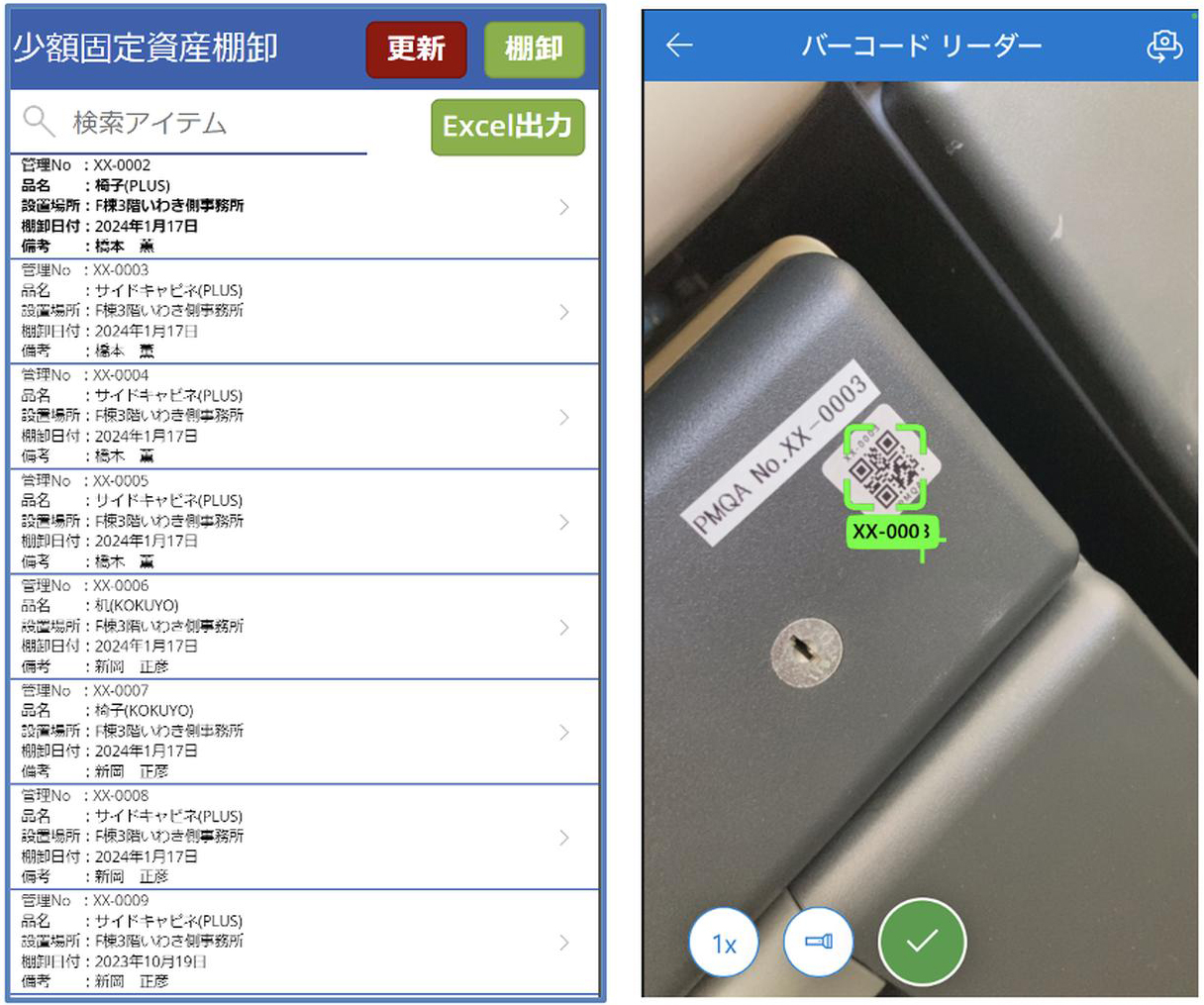
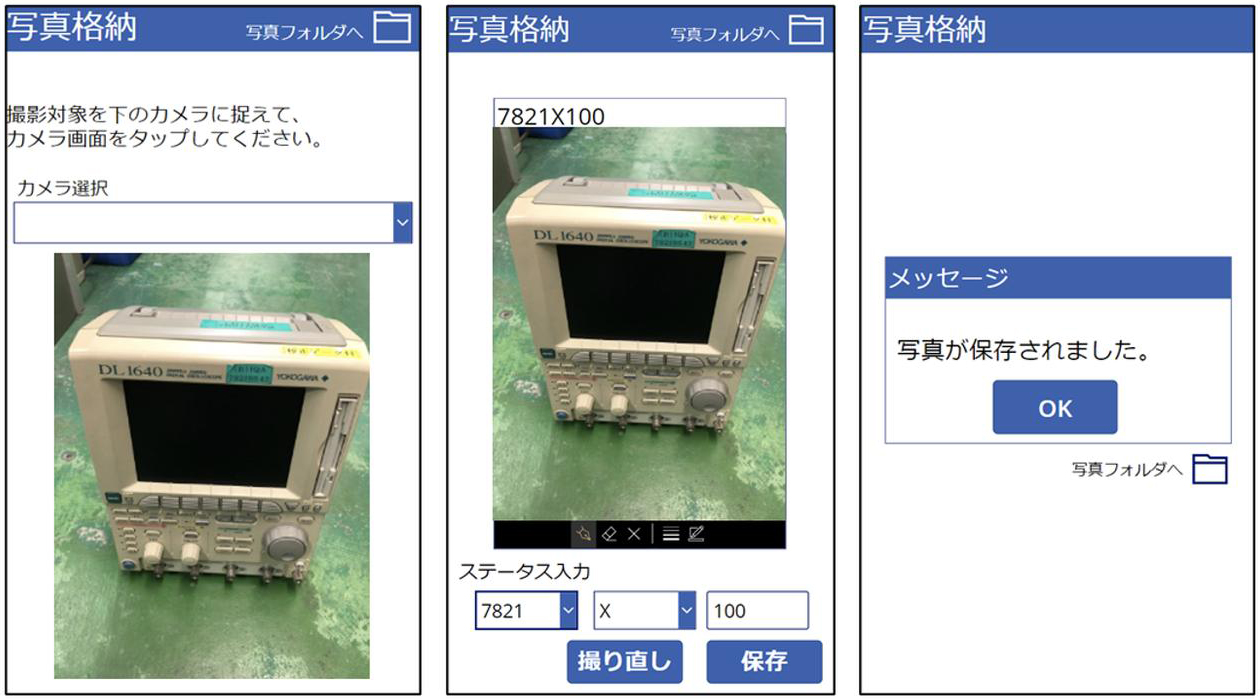
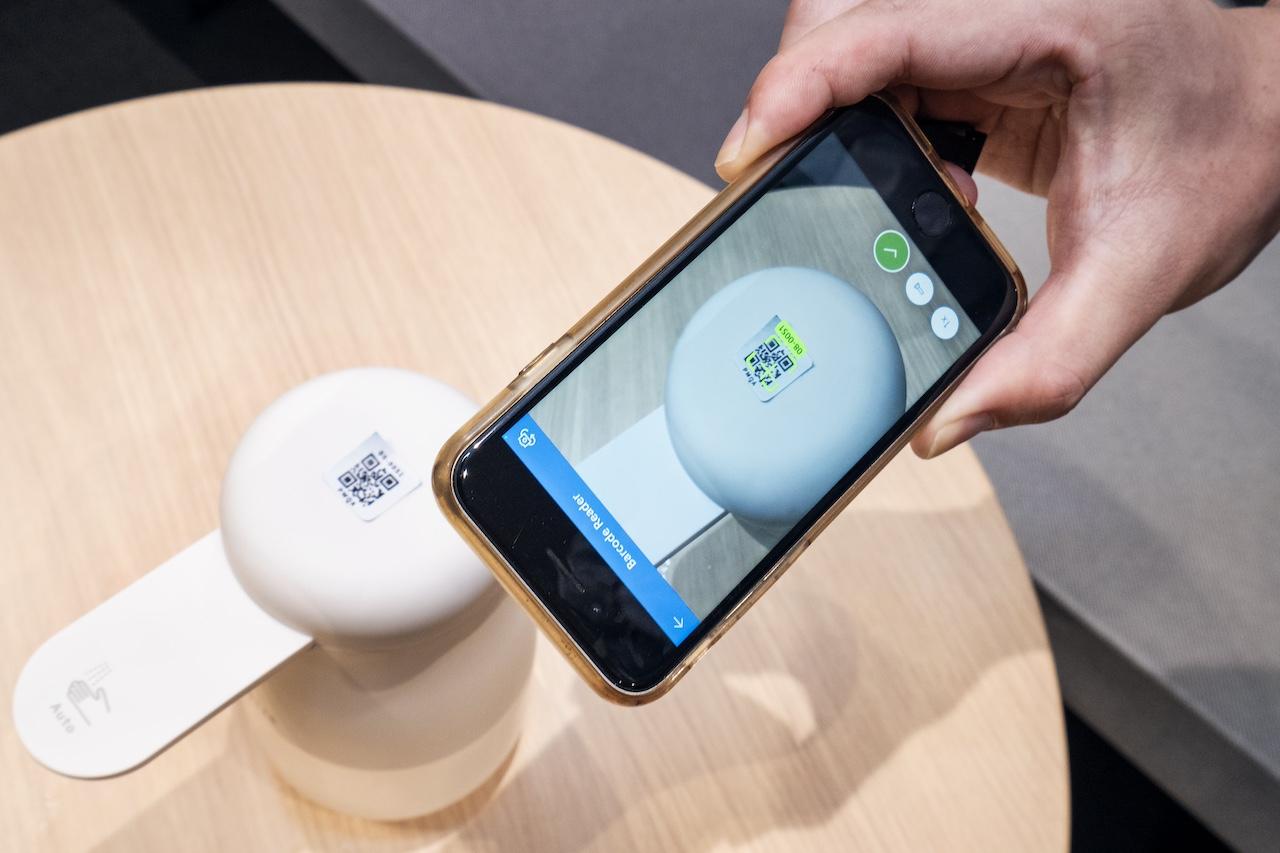
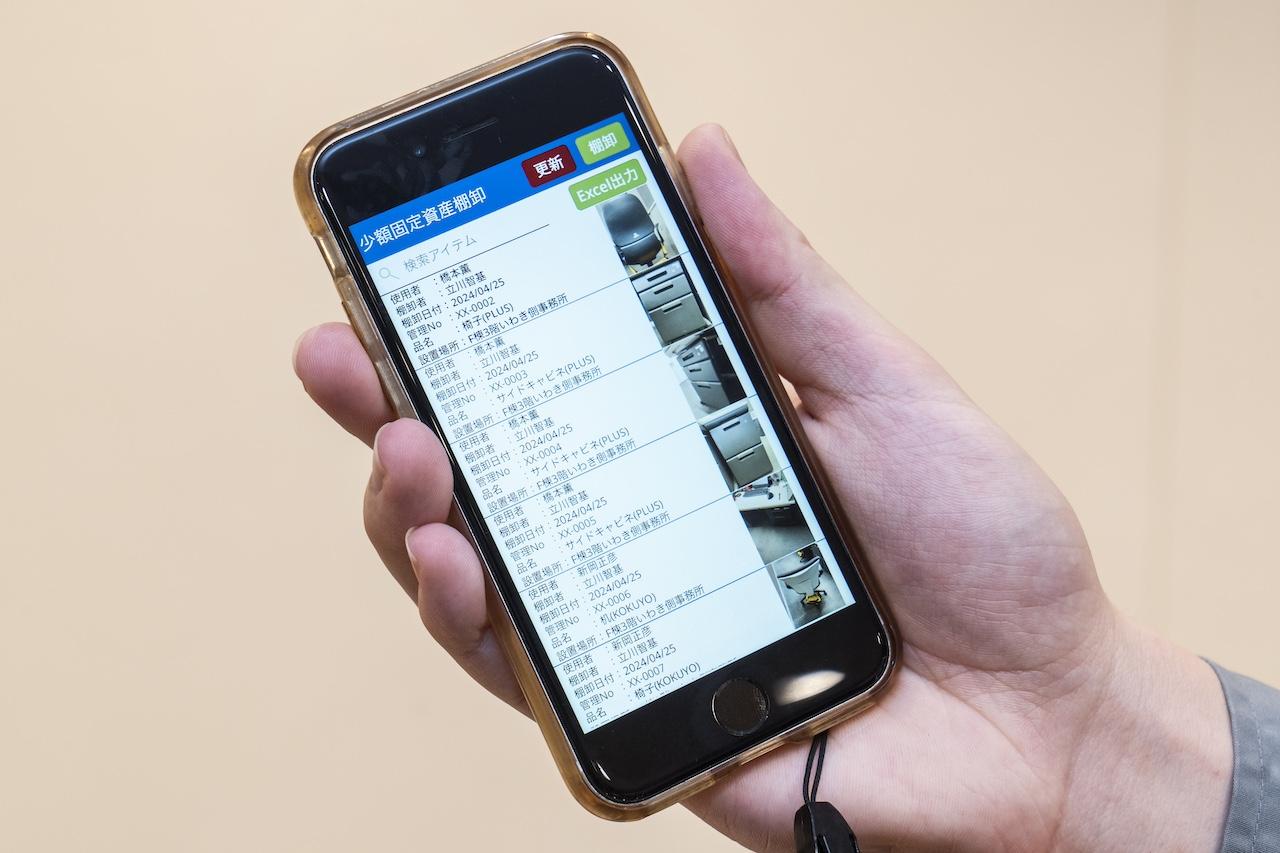
自動計測とデータ管理で、コンプライアンス強化
③の品質検査のデータを自動取得するシステムでは、計測データを自動取得して管理システムに格納することで、誤記などコンプライアンスリスクの低減と検査業務の効率化を両立させました。(2022年度から本格運用)
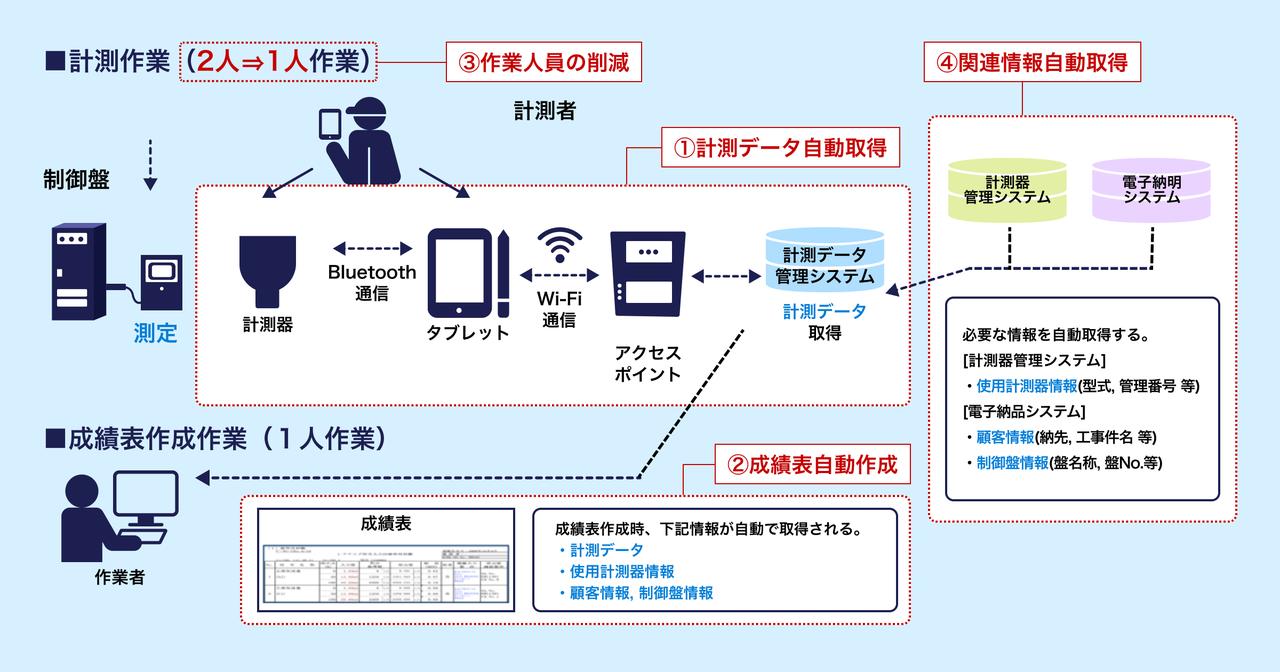
計測されたデータは自動でPCに取り込まれる
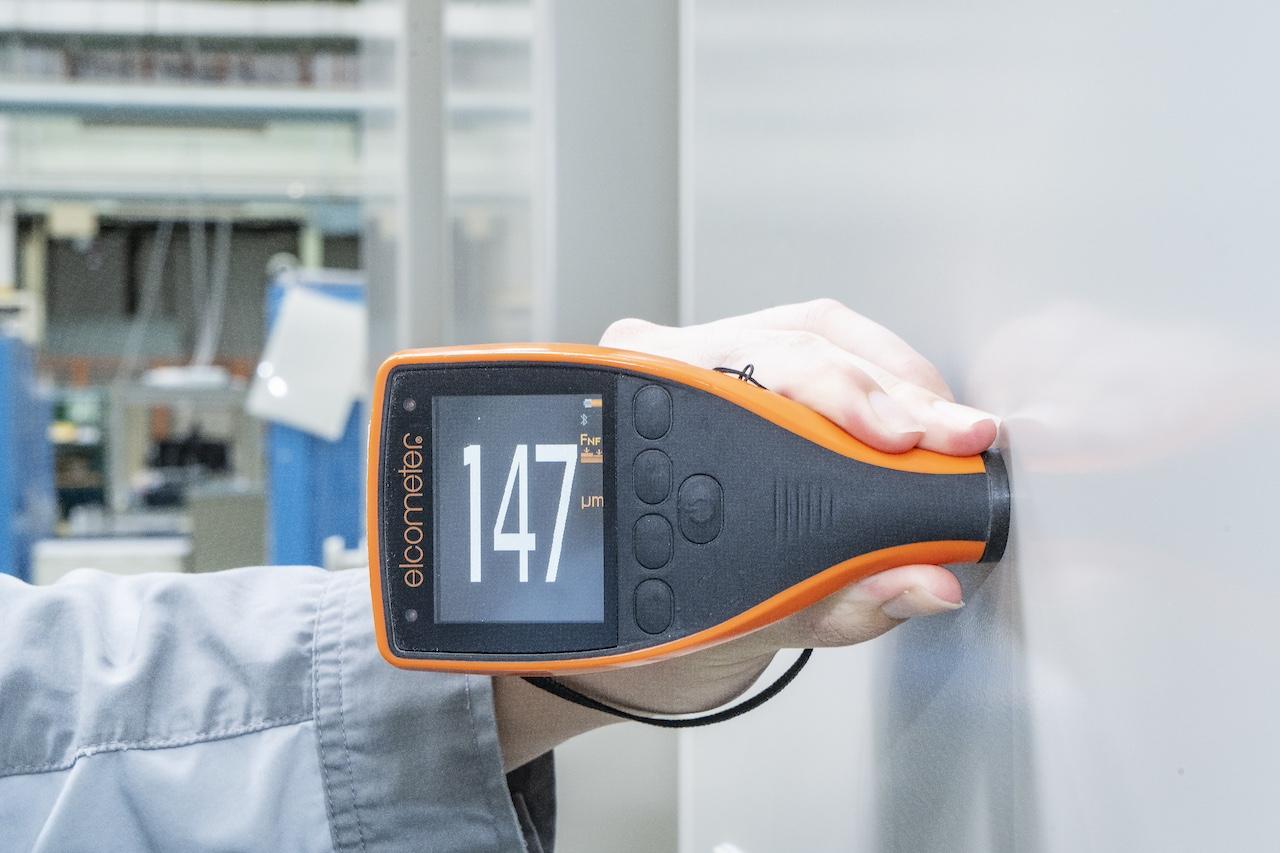

生成AIでナレッジ活用も高速かつ高度に
④の生成AIを利用したナレッジの情報検索システムは、従来数多く規格・規準から探していた作業を生成AIが瞬時に行ってくれるものです。また、蓄積したナレッジ・ノウハウも提示してくれるなど複雑なことまで対応可能です(現在開発中)。
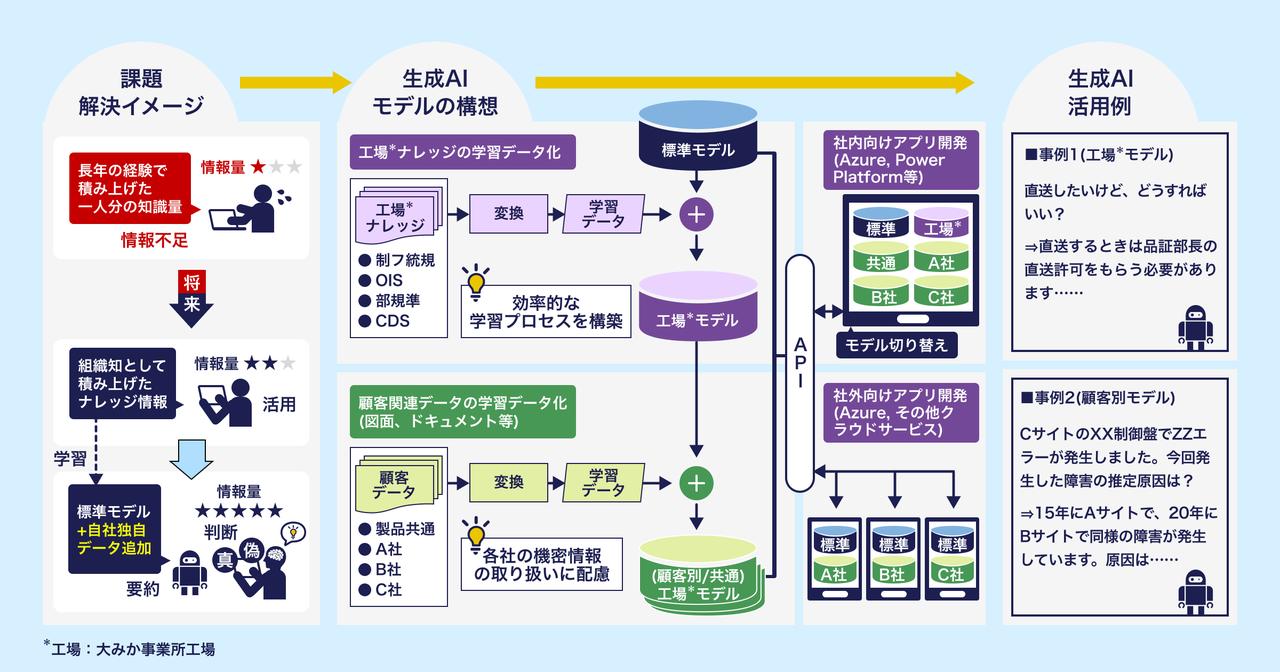
デジタルペーパーで検査品質が向上
⑤のデジタルペーパーを用いて検査品質向上と作業見える化を実現したシステムは、2024年度から本格運用しています。図面のチェック漏れの自動判別機能を利用して検査品質を向上させました。
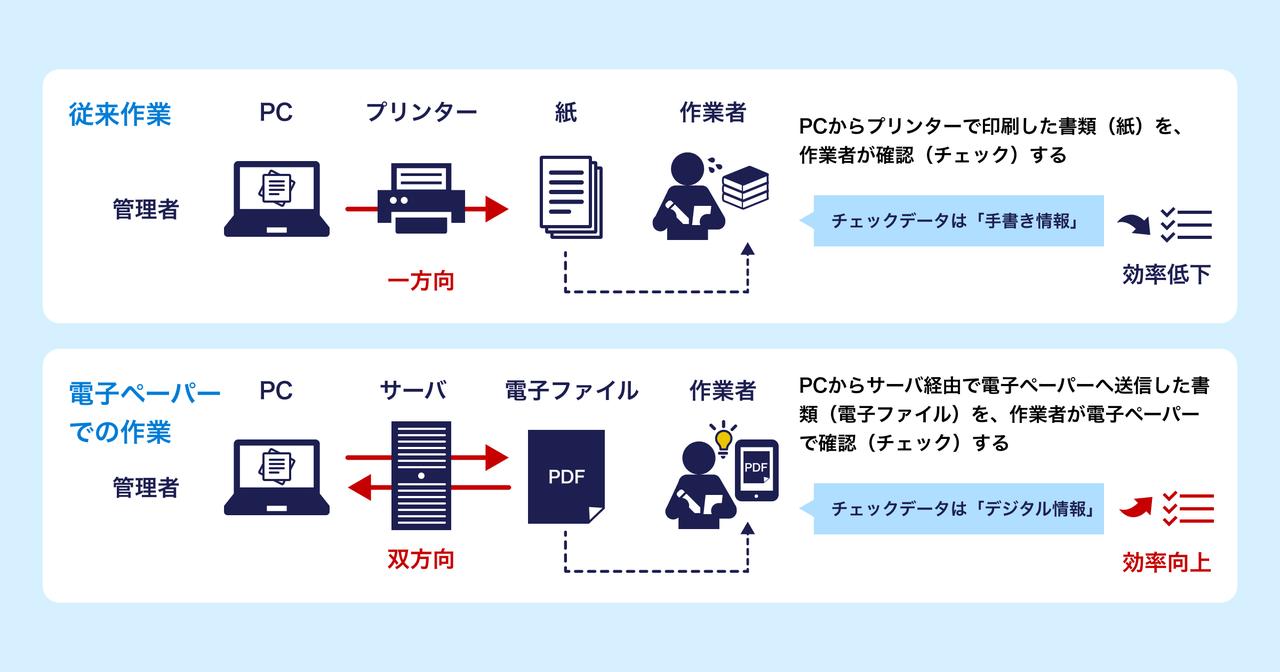
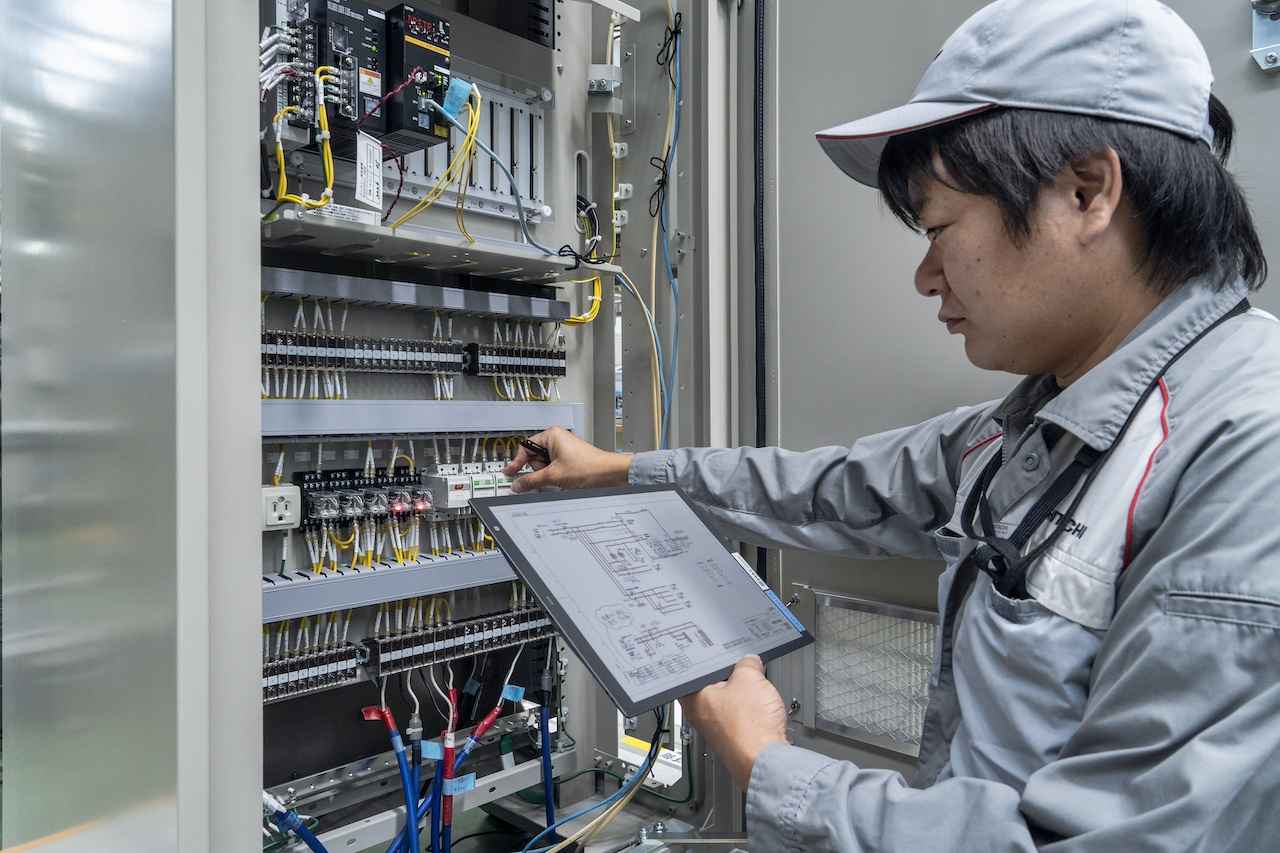
スマートグラスで作業を高度化・効率化
⑥のスマートグラスはメガネのようなアイウェアに作業手順書や図面などの情報を表示するものです。スマートグラスにより、リアルタイムで作業指示など必要な情報を確認しながら作業できます。図面がある場所まで移動したり、手に図面を持ったりすることなく作業に集中できます。
スマートグラスを使った作業の様子
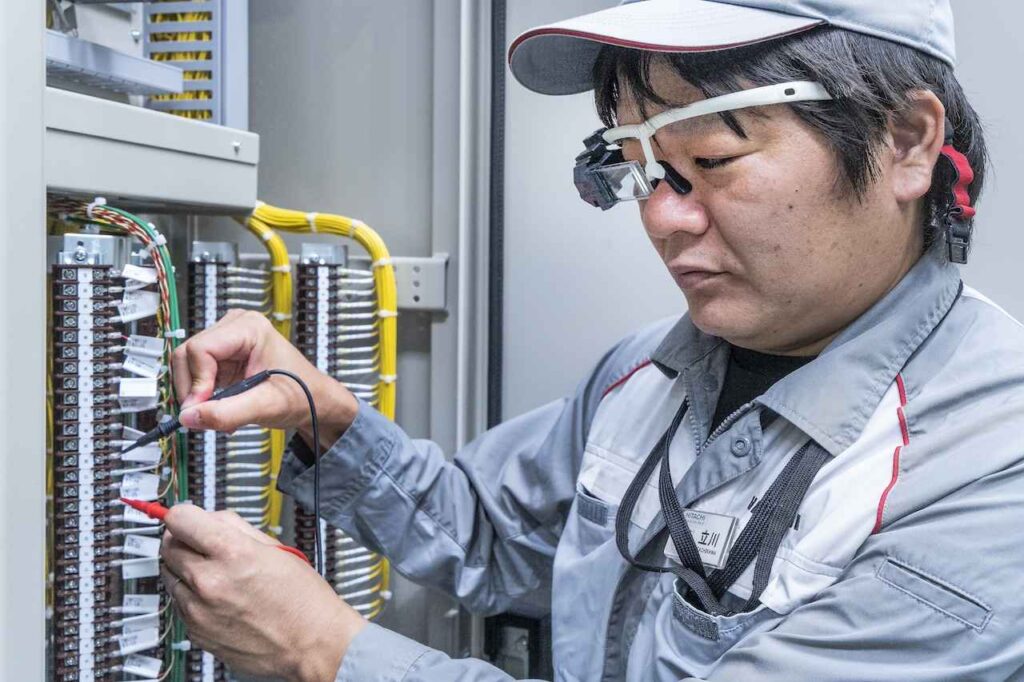
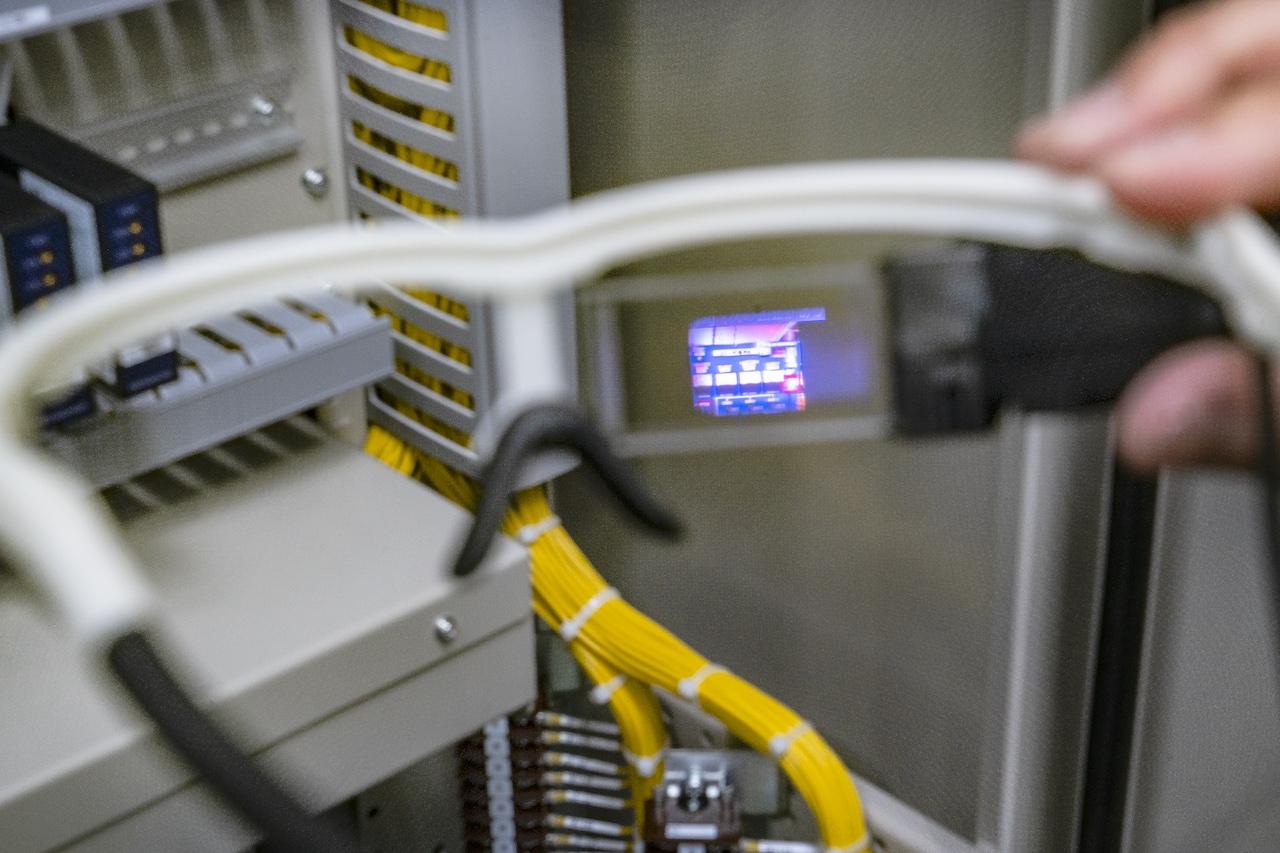
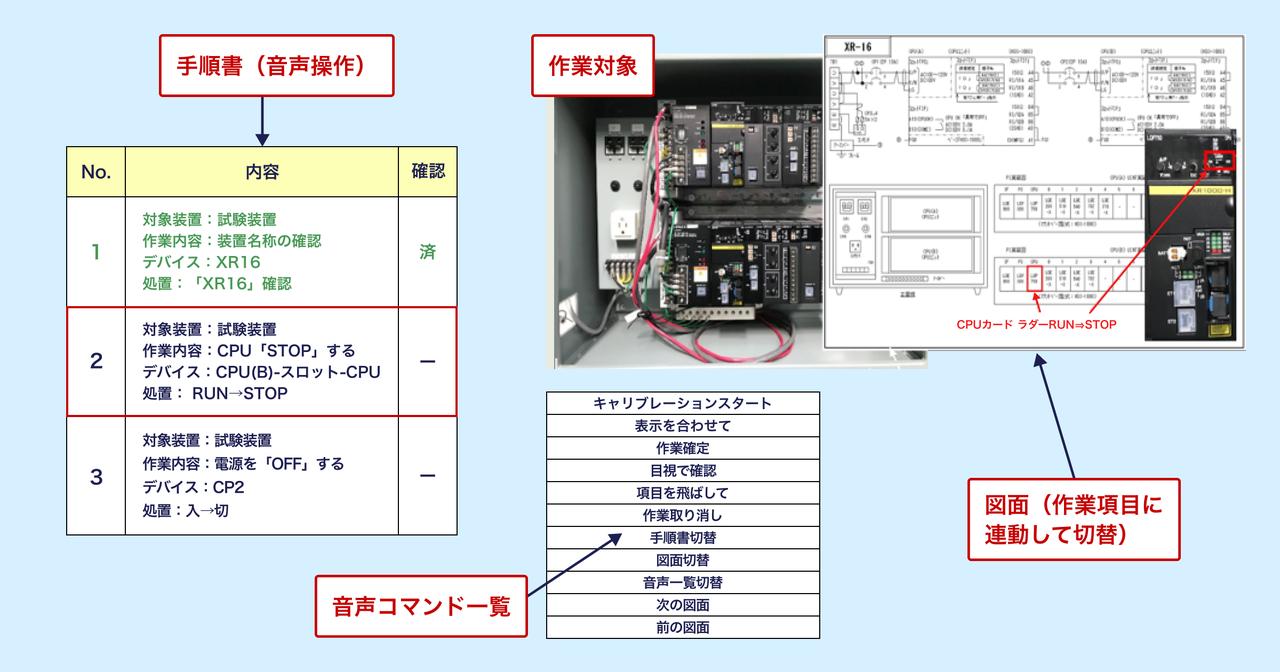
DX化に対する現場の空気を変えたデジタルペーパー導入時の施策
紹介した6つの取り組みのうち、実用化に向けて積極的に利用されているのはデジタルペーパーです。紙の使い勝手の良さを残しながら、チェック漏れ自動判別機能を使えば「人によるチェック漏れ」を解消できるほか、ペーパレスによるコスト削減や、情報をリアルタイムに管理する作業見える化(進捗確認)など多くのメリットがあります。
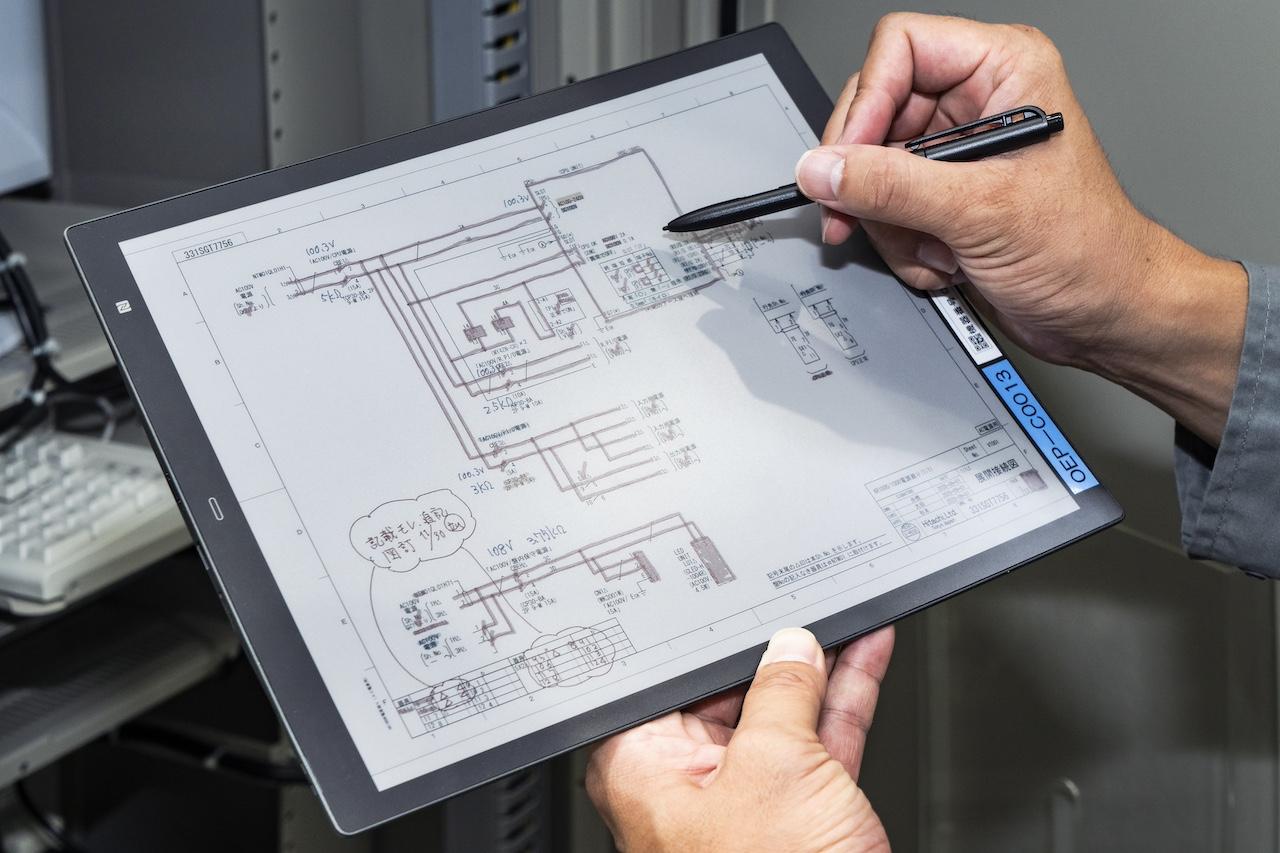
デジタルペーパー導入時に心配したのは「紙ならではの良さ」を手放すことへの拒否反応です。例えば、通常のタブレットでは表面が平滑で、紙と異なるタッチに違和感があります。これだけでも使ってもらえないのではないかと危惧したのです。しかし、デジタルペーパーは紙の感触を再現しているため書き心地に問題はありません。また、タブレットより軽いため現場で扱いやすく、イニシャルコストはタブレットの約半分のため導入しやすかったのです。
なお、紹介したデジタルペーパーは、同分野のパイオニアであるE Ink Holdings Inc.およびその子会社のLinfiny Japanと日立(大みか事業所および研究所)で協業して開発を推進しているものです。E Inkの最先端技術の4096色13.3″フレキシブルカラーデジタルペーパーディスプレイを搭載したデジタルペーパー端末は、NFCを内蔵し、超低消費電力で長時間の連続使用が可能。製造現場のニーズに対応したペン入力や、LinfinyのDCSS(Digital Paper Control Server Software)を活用したクラウド/オンプレシステム連携により、上位システムと複数のデジタルペーパー間でのドキュメント管理が実現できます。
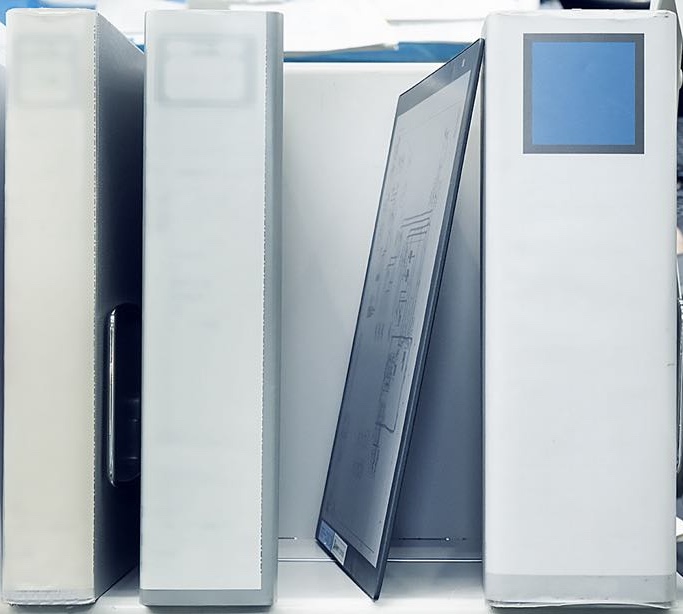
現場の抵抗感を払拭しようと奮闘した当時の様子を話すのは、このプロジェクトを推進した新岡正彦です。「自動でチェック漏れの確認をしてくれること、作業者や作業内容を時系列で記録できることなど、まずはメリットを伝えました。当初は個人のメモ帳やスケジュール管理などに使ってもらい、良さを実感してもらったのです」。
今は、作業者は多くの資料を抱えて現場に行くことがないなどのメリットを感じている一方、紙のようにめくれなかったり、複数のページを同時に見られなかったりという改善点もあります。これは今後の課題です。
品証デジタライゼーションの取り組みが進んだ理由
日立製作所グループ内には日々先進的な技術を追求する研究所があります。今回のように、研究所から「こんな技術があるのだがやってみないか?」という提案でスタートする実証実験も数多くあります。このように、研究開発部門と現場が一緒に試行錯誤したことで、今回のプロジェクトは順調に進みました。
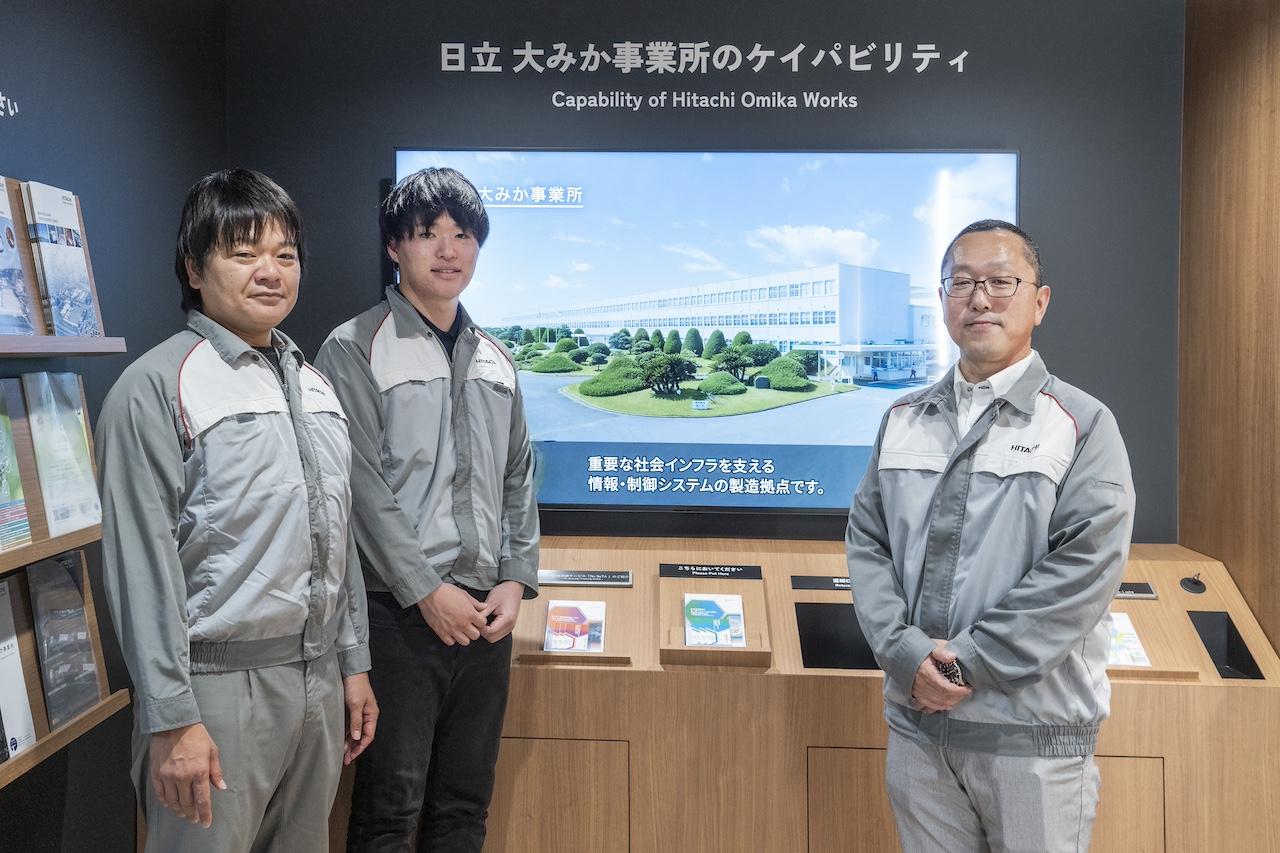
日立製作所では、今後も部署の垣根を越えたDXの取り組みで、さらなる業務改善を推進していきます。